ШУ «Молодогвардейское» в 2012 году сможет преодолеть миллионный рубеж по выдаче на-гора коксующегося угля - Газета

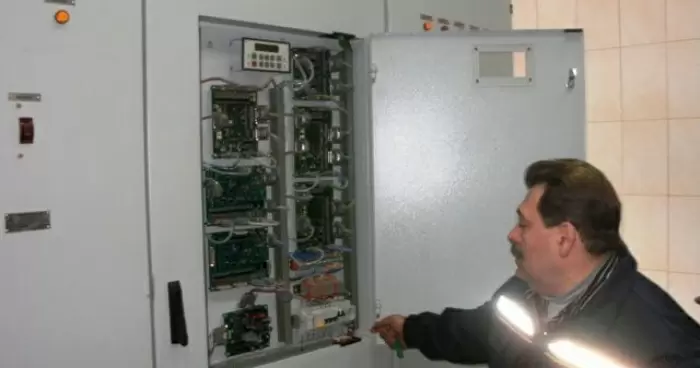
Шахтоуправление «Молодогвардейское» после запуска новой добычной лавы в 2012 году уверенно сможет преодолеть миллионный рубеж по выдаче на-гора коксующегося угля.
Как пишет издание Луганского областного совета "Наша газета", этим коллектив еще раз докажет, что готовить подходы к угольным пластам, добывать «черное золото» на основной одноименной шахте управления умеют. Ее слава ковалась в советские времена, но и сейчас трудовой коллектив возвращается на завоеванные позиции. Залог этого — высокий профессионализм и самоотдача рабочих, инженерно-технических работников, а также модернизация производства — как подземного, так и поверхностного.
Вот дошли, как говорят, руки, и до усовершенствования подъемных механизмов. Их здесь несколько.
С помощью одного из них и выходят на поверхность все добытые горняками миллионы тонн угля. Но лет ему столько, сколько и всей шахте. Хорошо еще, что некоторое обновление оборудования в семидесятые годы прошлого столетия продлило его жизнь до настоящего времени. Крутятся огромные подъемно-спускные барабаны, машинисты подъема по-прежнему вручную тормозят и разгоняют их, канаты накручивают сотни и тысячи километров. Все это работает безупречно, как и наметил это проект запущенной в производство много десятилетий тому назад шахты.
Но жизнь, а точнее, экономика, требует новых подходов в организации любого производства. В те времена электроэнергию для шахт никто и не думал экономить. А ведь весь подъем угля на-гора — на электрике. И стоит она сегодня миллионы пусть и не настоящего золота, а «черного», но все равно очень дорого.
Поэтому подъем № 2 и решили усовершенствовать в первую очередь. Всю механику — канатные барабаны, редукторы, электромоторы — оставили прежней, ведь ей еще работать и работать, лишь с эпизодическими незначительными ремонтами. А вот всю технически и морально устаревшую электрическую часть привели в соответствие с научно-техническим мировым прогрессом и идеологией энергосбережения.
Рассказывает начальник участка подъемного комплекса Валентин Матюхов:
— На внедрение новой аппаратуры в этом здании потратили шесть миллионов гривень. Собственно аппаратура стоила менее четырех миллионов, два миллиона пошли на ее приспособление к действующему оборудованию и наладку, 400 тысяч — на ремонт машинного зала. Экономический эффект от внедрения системы выражается экономией электроэнергии в год на полтора миллиона гривень. Можно просто легко подсчитать, что все затраты окупятся в течение четырех лет.
Далее. Облегчается труд машинистов подъемных машин (их в этом зале две. — Ред.), поскольку движение канатных барабанов происходит в автоматическом режиме, по необходимости переходят и на ручной. Это, в свою очередь, снижает нагрузку на канаты, на механизмы, особенно на коренную часть, на редукторы.
— Что же до этого было? — спрашиваю у механика Матюхова, как нам рассказали, всю свою жизнь (29 лет) проработавшего на этой шахте.
— Скорость подъема скипов с углем (скип — это подъемный со-
суд, предназначенный для транспортировки полезных ископаемых и породы с горизонтов шахт на поверхность по вертикальным или наклонным стволам. — Ред.) от этого не увеличилась, да такая цель и не ставилась. Она нас устраивает. Важнее то, что «сглаживаются» разгон каната и его остановка. Ведь вес одного скипа — одиннадцать тонн, в течение суток одна машина поднимает нередко более двухсот скипов, а обе выдают на-гора 4000 тонн угля...
Валентин Владимирович также рассказал "Нашей газете" о том, что копер, в котором движутся скипы, упирается в горизонт 680 метров. Хотя уголь добывается уже на глубине 900 метров. Он по конвейеру подается к нижней отметке копра и здесь грузится в скипы. Длина подъемного каната — также 900 метров. При этом учитывалась длина копра и необходимые запасные пять витков на подающе-принимающем барабане. Срок службы каната незначительный — четыре года. Учитывая ту нагрузку, которую испытывает канат, контроль его состояния проводится регулярно и очень тщательно.
О том, как велась замена электрической части подъемных машин, рассказывает представитель Павлоградского (Днепропетровская область) пуско-наладочного предприятия Юрий Кухаренко. Вместе с тремя своими коллегами и четырьмя представителями харьковского завода-изготовителя электронной аппаратуры они смонтировали всю систему управления подъемными машинами. Именно эта система и экономит электроэнергию, с помощью которой уголь поднимается на-гора:
— Не буду утруждать читателей терминами и рассказом о выполняемых электроникой функциях, приведу лишь образное и понятное многим сравнение с работой автомашин — с механической трансмиссией и с автоматической коробкой передач. Вот приблизительно такое улучшение произошло и на этом подъеме…
Как рассказал далее Юрий Кухаренко, это не единичный пример применения такой системы в «Краснодонугле». Подобная уже больше года функционирует на шахте имени Баракова, а также на ряде шахт она внедряется на системе вентиляции подземных выработок, где экономия электроэнергии составляет 40 — 50 процентов по сравнению со старыми схемами подключения вентиляторов.
… Еще сегодня в этом зале работают строители управления «Краснодонстройресурсы». Это им благодарна оператор подъемных машин Елена Зиновьева, с которой мы разговаривали, а также ее другие коллеги, за то, что в операторских стало намного уютнее за счет обогрева помещения смонтированной строителями системой «теплый пол».
Как рассказал мастер участка этого предприятия Алексей Богданов, даже в самые сильные морозы нынешнего февраля (минус 27 — 28 градусов на улице) в помещении температура не опускалась ниже плюс двенадцати. Работники этого предприятия утеплили здание снаружи, установили пластиковые окна, выполнили ев-роремнт в помещениях под установку электронной и электрической аппаратуры для работы подъемников, сегодня заканчивают отделку таким же способом бытовых помещений — для приема пищи, душевой.
Если зимой здесь тепло, то летом — не жарко: будут работать кондиционеры. Как видим, на шахте позаботились не только о технике, но и о людях. На улучшение бытовых условий на этом подъеме потрачено 150 тысяч гривень. Пишет "Наша газета".